|
Newsletter January 2021 | Menu of Newsletters
Commercial Micro Manufacturing -
Dec.2020
The need for nano- precision has became
increasingly important in many fields of research and manufacturing, inducing
microelectromcs fabrication, laser/optical system applications and biological
research. This has meant that so too has the need for vibration Isolation
technology that better facilitates the operation of sensitive Instrumentation
such as
atomic force microscopes, scanning tunneling
microscopes,
laser interferometers and optical
profilers.
Once the mainstay for stabilizing academia's
and Industry's most critical microenginering instrumentation, pneumatic (gas or
air pressurized) vibration Isolation tables are today proving unsatisfactory in
isolating disruptive
low-frequency vibrations. There is a growing trend
for locating sensitive instrumentation in building to locations that are
subject to extremely high levels of vibration and this is a significant
stumbling block for pneumatic vibration isolation tables, meaning alternative
vibration isolation solutions are required.
Vibration
sources Nano-level instrumentation is sensitive to extremely small
payload vibrations that can be caused by a multitude of factors. Every
structure (building) transmits vibrations from Internal and external sources In
a building, heating and ventilation systems, fans, pumps and elevators are Just
some of the mechanical devices that create vibrations. Outside a building,
adjacent road traffic, nearby construction, aircraft and even wand and other
weather conditions all create vibrations How strongly the instrumentation is
influenced depends on where it is in the building and how far away it is from
the vibration sources.
Isolation for vibration critical applications Over the
past 25 years, two technologies have gained prominence for their ability to
Isolate vibrations Influencing nano-level Instrumentation, namely active
vibration isolation (also known as electronic-force cancellation) and
negative-stiffness vibration isolation {also known as passive vibration
isolation).
Both active and negative-stiffness vibration isolation are
uniquely equipped for applications where structures smaller than a micrometre
need to be produced or measured. These technologies provide functionality that
is typically not achievable with pneumatic vibration isolation
tables.
Full article: Comparing systems... |
MK26 Ergonomically
Designed Ultra-Low Frequency Table &
Workstation
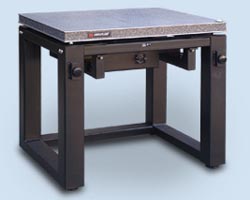
The
MK26 Series Vibration
Control Workstation with more ergonomic comfort is designed specifically for
ultra-low natural frequency applications. The system utilizes MinusK patented
negative stiffness vibration isolators in order to provide a compact, passive
Vibration Isolation Workstation with ultra-low natural frequencies, higher
internal structural frequencies, and excellent vertical and horizontal
isolation efficiencies. The MK26 has also been upgraded to provide much better
user comfort and additional leg space.
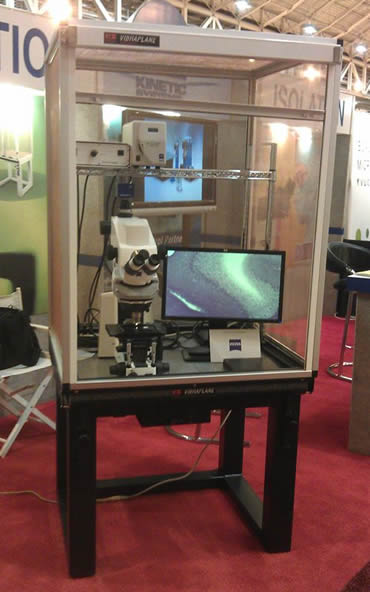 Acrylic Chamber atop an
MK26
Pricing & sizes for
MK26
|
You might have thought, maybe for only a
few moments, that your
audio system was
sounding especially good. With that feeling, you would have rated the sound a
top score of "10". Then those magical moments ended and your system returned to
it's normal - but still good - performance level. Well, folks, the Minus K
CT-2 Isolation
Platform could raise your system score to an "11" and keep it there! Highly
recommended for systems that are already high performance and where you want to
coax the maximum performance from your audio investment....
Dr. David L.
Platus is President and Founder and is the principal inventor of the
technology. He earned a B.S. and a Ph.D. in Engineering from UCLA, and a
diploma from the Oak Ridge School of (Nuclear) Reactor Technology. Prior to
founding Minus K® Technology he worked in the nuclear, aerospace and
defence industries conducting and directing analysis and design projects in
structural-mechanical systems. He became an independent consultant in 1988. Dr.
Platus holds over 20 patents related to shock and vibration
isolation.
Ultra-Thin 2.7" High
CT-2 Product
Attributes: - Isolation performance is typically 10 to 100 times
better than air systems - No air or electric power is
required - Nothing to wear out - No
maintenance
A complete description of the patented
Negative-stiffness design can be found on the
Technology page of the manufacturers Web site. The Minus K platform is
completely silent and requires no pumps or power. The
CT-2 model platforms
are available for different weight ranges of payload, or supported weight. The
40CT-2 model, while not specifically listed on the Web page, was perfect for
the Clearaudio Ovation
turntable used for
this review. The platform dimensions are 18" W x 20" D x 2.7" H, with a weight
of about 30 pounds. Different models, for different payloads, range in price
from $4,650 to about $5,250. In my system, the platform was installed 20" W x
18" D, which placed the adjustment crank on the 18" left side.
The
horizontal frequency of ~1.5 Hz is achieved at or near the upper limits of the
payload range. The vertical frequency is tunable to 0.5 Hz throughout the
payload range. What this means is that any very low frequency vibrations that
are not blocked or absorbed by the Minus K platform are several orders of
magnitude below what your phono cartridge, or even the best subwoofers, can
process.
Full article... |
3D Surface Analysis Vibration
Isolation High-precision, nanometer-level 3D surface
measurement systems can be negatively affected by low-frequency
vibrationdistorting imaging and producing inaccurate measurement
readings. |
Manufacturers need to control processes to
produce a consistent, reliable product. Where precision surface engineering is
required, surface measurement may be a key part of maintaining control of the
process, by checking output to see that the process is not outside of
specification.
3D non-contact surface analysis is widely used in the
industry for the measurement of small displacements and surface irregularities.
It delivers the ultimate in high accuracy and repeatable and traceable
measurement. When built into microscopy equipment, employing 3D laser scanning
or structured light, these systems report the surface condition of a product
with more accuracy than any other methodproviding nanometer-level profile
measurements of height, width, angle, radius, volume, and roughness. Such
precision measurement systems allow users to improve product quality and
reliability, and increase manufacturing consistency and production
yields.
Low-Frequency Vibration When measuring at such high
levels of precision, any instrument can be negatively affected by low-frequency
vibrations generated within a manufacturing facility. These can distort
measurements and impact imaging and measurement data
One company that
has great familiarity with the manufacturing environment and 3D surface
measurements is Keyence Corporation--a leading supplier of sensors, measuring
systems, laser markers, microscopes, and machine vision systems
worldwide.
We have many customers with high-precision 3D measurement
systems operating in high-vibration environments, performing microscopy
evaluation at 30,000 times magnification, looking at nanometer-level surface
features, said Evan Eltinge, Senior Sales Engineer Surface Analysis Team, with
Keyence Corporation of America. At that level of detail, and in that
environment, if measures are taken to reduce vibration it improves the quality
of the data.
Without proper isolation surface measurements occurring at
3,000 to 5,000 times magnification, the vibration could contribute to image
blurring and loss of image quality, continued Eltinge.
Vibration can be
caused by a multitude of factors within a plant; every structure is
transmitting noise. Within the building itself, production machinery, forklift
trucks, the heating and ventilation system, fans, pumps, compressors, and
elevators are just some of the mechanical devices and equipment that create
low-frequency vibration. Depending on how far away the surface measurement
instrumentation is from these vibration sources, and where inside the structure
the instrumentation is locatedwhether on the production floor or in a loftwill
determine how strongly the instrumentation will be influenced.
External
to the building, the equipment can be influenced by vibrations from truck
movement, road traffic, nearby construction, loud noise from aircraft, and even
wind and other weather conditions that can cause movement of the
structure.
Vibration Isolation Options for 3D Surface
Analysis...
Full article... |
The Moulé Group, at the University
of California/Davis, is interested in the solution processing and patterning of
organic electronic materials for use in devices such as light-emitting diodes,
photovoltaics, transistors, thermoelectric, and chemical sensors. The Group
specifically focuses on using structural and dynamic measurement techniques to
quantify the effects of solution processing and patterning on material
morphology and device architecture.
Tucker Murrey, a doctoral candidate
and published author with the Moulé Group, is actively involved with
researching and designing a scalable optical patterning process for organic
photovoltaic applications.
"Most working organic devices consist of
several layers of material, each having a specific optical and/or electronic
function," said Murrey. "One universal design constraint for complicated device
architectures, like organic field-effect transistors (OFETs), organic
photovoltaics (OPVs) and red-green-blue organic light-emitting diode (OLED)
displays is that they require multiple components patterned laterally and
vertically to operate. Currently, many of these components are comprised of
non-flexible inorganic materials. In order to move towards flexible, all
organic electronic devices, there is a need to develop high precision vertical
and lateral patterning methods that are compatible with solution processing.
mmense efforts in the plastic electronics field have led to
unprecedented progress and continuous improvements in organic photovoltaic
(OPV) performance.
"Given that conventional photolithography technology
techniques are incompatible with polymeric semiconductors, there is a critical
need to develop scalable photopatterning methods capable of laterally
patterning organic semiconducting compounds with sub-micromometer resolution,"
added Murrey. "This patterning process would enable the construction of a
sophisticated OPV architecture designed to increase external quantum
efficiency."
"A scalable process for controlling film topography with
sub-micrometer resolution would represent a substantial development that
enables the advancement of complex organic electronic device architectures,"
continued Murrey.
Photothermal Projection Lithography The
Moulé Group is working on a series of solution-based methods, one of
which is called Photothermal Projection Lithography for Polymeric
Semiconductors with Sub-diffraction Limited Resolution.
Polymeric
semiconductors combine many of the electrical properties of inorganic
semiconductors with the mechanical flexibility and chemical processability of
organic materials, such as enabling them to be deposited from solution over
large areas, greatly reducing production costs compared to conventional
metallic semiconductors. Developments like this have motivated a rapid increase
in demand for low-cost, high-throughput, and high-resolution fabrication
techniques.
Organic semiconductors are non-metallic materials that
exhibit semiconductor properties, whose building blocks are polymers made up of
carbon and hydrogen atoms. These conductive polymers are, essentially,
electrical insulators, but become conducting when charges are either injected
from electrodes or by photoexcitation, or doping the intentional introduction
of impurities into an intrinsic semiconductor for the purpose of modulating its
electrical, optical, and structural properties.
"Over the past year I
have been upscaling an optical patterning process that our group developed to
make micro-scale electronic devices with these materials," expressed Murrey.
"The overall pattern area was limited to less than one square millimeter. Now
we are trying to upscale the overall patterning area to about one square
centimeter."
Murrey designed a unique lab-scale photolithography system,
modifying a Leica DM2700 optical microscope, swapping out its LED illumination
source to permit a high-powered (Class 4) 405nm diode laser to be projected
through it. Built into the system is a laser beam expander, collimating lens,
and an optical speckle remover.
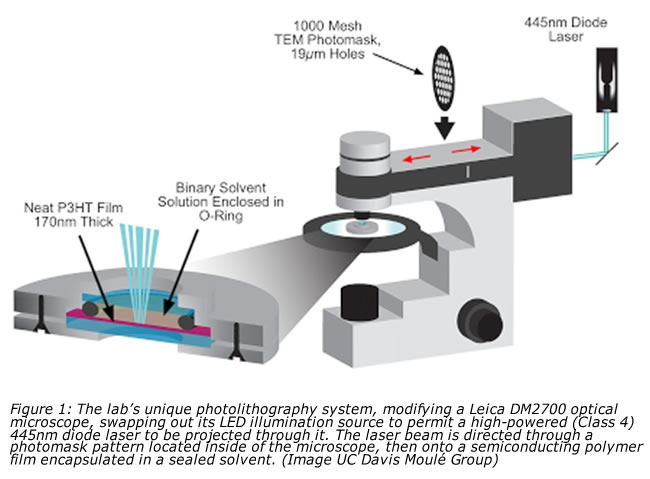 |
Full article... |
For decades, pneumatic air tables have been
the workhorse for reducing vibrations in cleanrooms for manufacturing and
research, where critical micro-engineering instrumentation is employed. But
just as technology has steadily pushed the boundaries into nano-applications in
microelectronics fabrication, industrial laser/optical systems and biological
research, so has the need become ever more necessary for improved precision in
vibration isolation.
Increasingly, pneumatic air tables are taking a
back seat to the more recent technology of negative-stiffness vibration
isolation, which over the past 20 years since its introduction, has proven
itself in thousands of applications throughout industry, government and
academia, including some of the most diverse and challenging environments, such
as cleanrooms.
Vibration Sources Vibration can
be caused by a multitude of factors. Every structure is transmitting noise.
Within the building itself, the heating and ventilation system, fans, pumps and
elevators are just some of the mechanical devices that create vibration.
Depending on how far away the cleanroom equipment is from these vibration
sources, and where in the structure the equipment is located, whether on the
third floor or in the basement, for example, will determine how strongly the
equipment will be influenced. External to the building, the equipment can be
influenced by vibrations from adjacent road traffic, nearby construction, loud
noise from aircraft, and even wind and other weather conditions that can cause
movement of the structure.
Vibrations in the range of 2 hertz (Hz) to
20,000 Hz will influence sensitive equipment. But these internal and external
influences primarily cause lower frequency vibrations, which are transmitted
through the structure, creating strong disturbances in precision equipment used
in cleanrooms.
Vibration Isolation Used
extensively in semiconductor manufacturing, biotechnology, the life sciences,
and other fields that are very sensitive to environmental contaminants - such
as dust, airborne microbes, aerosol particles, and chemical vapours -
cleanrooms provide an enclosed environment with a controlled level of
contamination that is specified by the number of particles per cubic metre at a
specified particle size.
Equipment employed inside the cleanroom must be
designed to generate minimal air contamination including vibration isolation
equipment, which can range from relatively simple rubber blocks, metal springs
and breadboards, to highly efficient air systems, active electronic systems,
and negative-stiffness systems - constructed with more advanced technologies
and materials for higher precision vibration isolation.
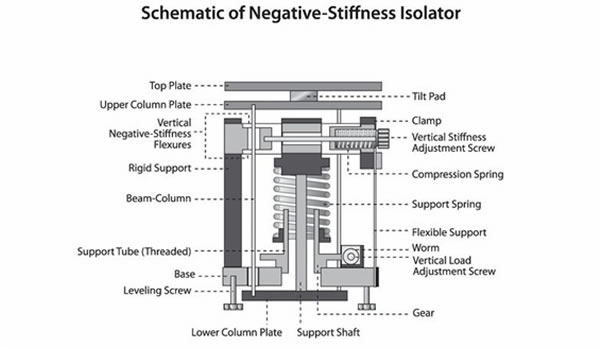
Full article... |
 |
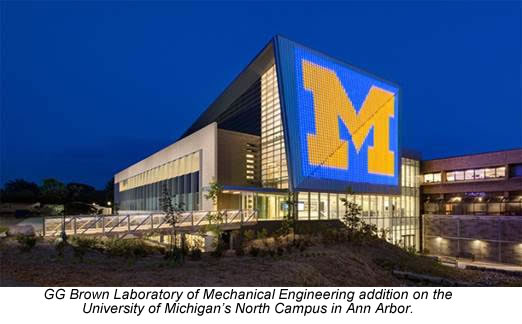 |
The Ultra-Low Vibration Lab (ULVL) is a
part of the new Center of Excellence in Nano Mechanical Science and Engineering
(NAMSE) a recent addition to the G.G. Brown Laboratories on the North
Campus of the University of Michigan in Ann Arbor. Noel Perkins, former
associate chair for Facilities and Planning with the Department of Mechanical
Engineering, describes this addition as a
building-within-a-building. The Nanoengineering Lab, located
on the ground floor, contains eight ultra-low-vibration chambers for
nanoscale metrology, mechanical, temperature and interference
testing.
The chambers are structurally isolated from the balance of the
building. Vibration isolation tables are mounted on pillars that are part of an
8-ft-thick seismic mass, which is isolated from the chamber floors. Even
researchers footsteps wont disturb experiments. With the emergence of
nanotechnology and nanoengineering of the last two decades, a relatively small
number of institutions and agencies have been able to construct facilities for
ultra-sensitive measurements, and I know of none that are focused on the
mission of a mechanical engineering department, said Edgar Meyhofer, professor
of mechanical engineering and biomedical engineering at the
university.
Validating Fluctuational
Electrodynamics When heat travels between two separated objects, it
flows differently at the smallest scales distances on the order of the diameter
of DNA, or 1/50,000 of a human hair. For example, heat radiates 10,000 times
faster at the nanoscale. Researchers have been aware of this for decades, but
they have not understood the process. Now, at ULVL, researchers have measured
how heat radiates from one surface to another in a vacuum at distances down to
2 nanometers. "We've shown for the first time, the dramatic enhancements of
radiative heat fluxes in the extreme near-field," said Reddy. "Our experiments
and calculations imply that heat flows several orders of magnitude faster in
these ultra-small gaps." Reddy and Meyhofer led the work. A paper on the
findings was recently published in the international journal of science,
Nature.
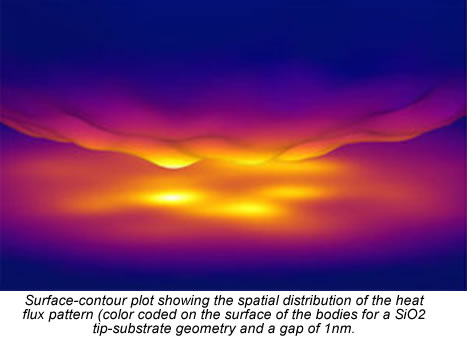
Full article... |
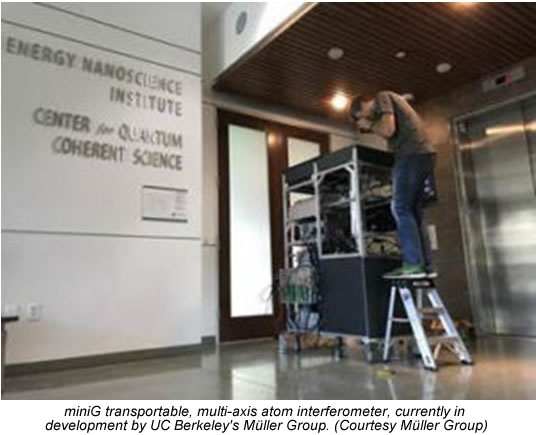 |
Professor Holger Müller's Group at UC
Berkeley is focused on advancing experimental quantum technology to push the
sensitivity of experiments to new levels, and to perform precision measurements
of fundamental constants. The groups work uses methods from atomic, molecular
and optical physics. One project is the development of a transportable,
multi-axis atom interferometer, named miniG.
MiniG was designed to
research how quantum interference can be used to measure gravity outside of the
laboratory. When cooled to just above absolute zero, the atoms form the focus
of a portable quantum gravimeter.
Gravimeters, used to measure
gravitational acceleration, have been successfully applied for metrology,
geology and geophysics. MiniG uses an atom interferometer to measure the effect
of gravity on clouds of atoms that are first trapped and cooled. Interferometry
inherently depends on the wave nature of the object. Particles, including
atoms, can behave like waves. Atom interferometers measure the difference in
phase between atomic matter waves along different paths.
We use atoms
that are laser-cooled to millionths of a degree above absolute zero, said
Xuejian Wu, a post-doctoral scholar, involved in the development of miniG at
the Müller Group. With pulses of light, we drive each atom into a quantum
superposition of having been kicked with the momentum of photons, or not
kicked. The atoms, in two places at one time, are in a superposition of
recoiling backwards or staying still. By manipulating the state of the atoms
using one of two types of such light pulses, we steer the matter waves' paths
and recombine the matter waves at the end of the experiment.
Atom
interferometry has become one of the most powerful technologies for precision
measurements, and atomic gravimeters, based on atom interferometry, are
extremely accurate and have long-term stability.
Current atom
interferometers, however, are too complicated to operate in a miniature package
or under field conditions. Berkeleys mini-G was engineered to resolve this
issue.
In this project, we are developing a mobile atom interferometer
using a single-diode laser system and a pyramidal magneto-optical trap,
continued Wu. This allows the device to be smaller, simpler and more robust
than conventional atom interferometers.
Vibration
Isolation
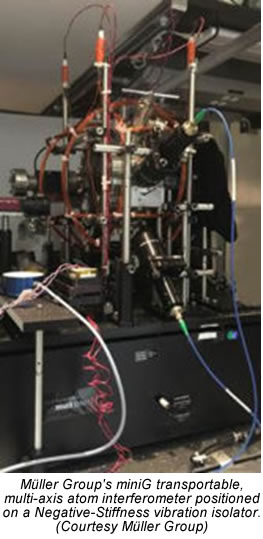
Measurements of atomic precision require
isolation from ambient vibrations coming from internal and external sources. As
measurements are being done at a smaller and smaller level, those vibrations
that are present will start to dominate, and the need for more effective
isolation increases.
Although the Müller Groups research
laboratory is situated in the basement of a building on the Berkeley campus, it
is still influenced by vibrations from the buildings HVAC system.
For
several years now we have been using
Negative-Stiffness vibration isolation for our
research projects, continued Wu.
Full article... |
|
|
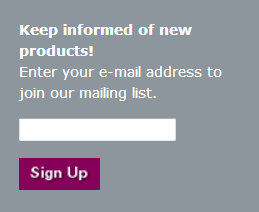
 |
|
|